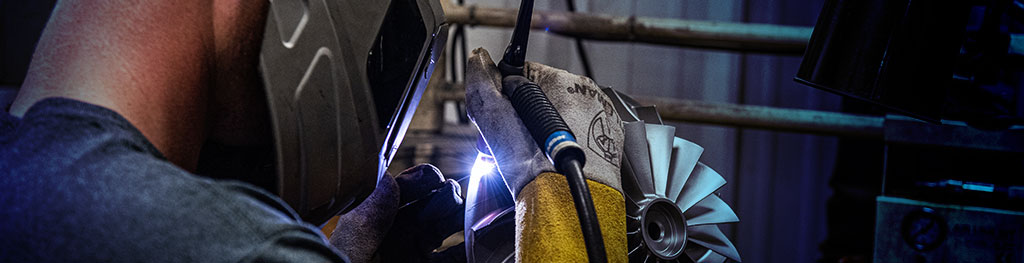
We also understand some of the biggest hurdles that frustrate businesses hobbled by a compressor’s failure and work to solve those problems every day. Here are a few:
More Accurate Bids
When we put out a bid for a job, it will be highly accurate and well-informed. We do our best to get as much information about your issue as possible to accurately diagnose the problem before we give you a price. We hear too often from disgruntled clients that the initial bid they are given ends up being much higher after the problem is assessed further. We just don’t think that’s right.
Better Turnaround
We know first-hand that if your compressor is down, it means loss of production. Yet, we’ve heard nightmare scenarios of months-long turnaround times to even get a service call answered. We think that’s unacceptable. We offer 24/7 emergency services because we know that you don’t have time for down time.
Integrity in our Products & Service
We are incredibly proud of our company and our team. Each and every one of them. That allows us to say with confidence whether it’s the parts you order from us or the services we provide, we stand behind them 100%. Our only job is to make sure you’re back up and running as quickly and safely as possible, and your satisfaction from a job well done is how we measure that. If you’re not happy, we didn’t do our job.
We just want to offer a better, faster and more reliable solution to what otherwise may be your only other option. From our previous experience in this industry, we recognized the need for better service, better turnarounds and better products. That’s why we started this company. We’d love to have the opportunity to show you we mean business.
If you have questions about our products, parts or services, we’d love the opportunity to chat with you about it. You can always reach us on the phone at (866) 383-0016, including for 24/7 emergency service. Or, just fill out the form and someone will get in touch with you.
A.C.E. vs OEM
Why should you choose A.C.E. for your compressor needs over the OEM? Here are a few reasons:
- Gear driven thin line Inlet Guide Vane Valves (IGV) for superior serviceability and longevity.
- All rotors are balanced to a lower spec than OEM.
- We offer a catalog of repairs from bearings to seals to rotor assemblies that the OEMs would require new parts for.
- Our response time and time frames are second to none.
- Non-proprietary controls for virtually all centrifugal compressors.
- Our controller out preforms every OEM offering and offers from a 3% to 5% energy savings.
- We offer services for every major brand and model of centrifugal compressors.
CENTAC specific benefits to choosing A.C.E.:
- Lifetime warranty on sleeved cooler barrels.
- Full stainless-steel sleeve on cooler barrels.
- A.C.E. air/oil seals are easily rebuildable due to snap ring design.
- More tubes per cooler for better CTD’s.
- Largest inventory of CENTAC coolers in North America.
- A.C.E.’s Gasket kits use Silicon in high temp areas and Viton in any area sealing oil.
- This is less expensive than the all Viton OEM kits and Silicon is better in high temp applications.
Atlas Copco specific benefits for choosing A.C.E. over the OEM:
- Our ZH bearings are rebuildable TPJ bearings rather than the throw away Flexure design.
- New replacement, programmable actuator for Atlas Copco inlet and bypass valves.
- Non-proprietary controls for Atlas Copco centrifugal compressors with Electronikon controls.